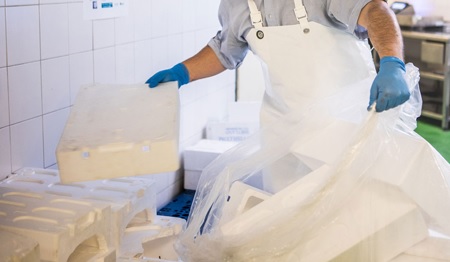
- Tras 3 años de investigación, esta iniciativa ha demostrado que, técnicamente, es posible reciclar las cajas de pescado de EPS y transformarlas en nuevos envases de poliestireno (PS) para aplicaciones en contacto alimentario.
- Y todo ello con los más altos grados de exigencia de la industria alimentaria y la EFSA.
- El proyecto abre paso a nuevos mercados de materiales reciclados de calidad, con el consiguiente beneficio ambiental.
Cerceda, a 4 de septiembre de 2020- El proyecto Life EPS-SURE culminó recientemente tras 3 años de investigación dedicados al reciclaje de plástico. Las cajas de poliestireno expandido (EPS), conocidas como corcho blanco, y utilizadas como envase para almacenar, transportar y presentar productos frescos, pueden transformarse, gracias a un innovador proceso de reciclado, en nuevos envases de PS aptos para contacto con alimentos. La iniciativa contribuye así a la apertura de nuevos mercados de materiales reciclados de calidad, con el consiguiente beneficio ambiental.
Se demuestra así la viabilidad técnica del proyecto, que abre paso a nuevos desarrollos y sienta las bases para la autorización y certificación de grado alimentario para el poliestireno reciclado procedente de la caja de pescado (r-PS) por parte de la agencia europea EFSA.
Asimismo, los test sensoriales organolépticos han sido superados ampliamente, no habiéndose detectado alteraciones debido a la posible presencia residual de aminas altamente odorantes que genera el pescado.
Coordinado por Cicloplast, han formado parte de esta iniciativa entidades tales como Cicloplast, Anape, Coexpan, El Corte Inglés y Total Petrochemicals Ibérica.
FASES
La primera fase del proyecto se inició con la recogida de los residuos de las cajas de pescado de EPS en algunos centros de El Corte Inglés, procediendo a la retirada de etiquetas y lavado de las mismas para eliminar restos orgánicos.
Posteriormente, estas cajas se embolsaron e identificaron para asegurar su trazabilidad y evitar así el riesgo de entrar en contacto con contaminantes.
Una vez trasladadas a un centro de compactación (de la empresa Saica), se transformaron en briquetas o bloques sólidos en una instalación específica y, desde allí, viajaron a un centro de pretratamiento.
La segunda fase se inició en la planta recicladora de Acteco, donde se trituraron las briquetas para convertirlas en copos de EPS, que fueron lavados en una solución alcalina en condiciones controladas de temperatura y tiempo, pasando a un proceso de secado por centrifugación y aire caliente. Una vez concluido el pretratamiento, se eliminaron parte de los contaminantes y aminas procedentes del pescado.
El material obtenido se transportó a las instalaciones de Total Petrochemicals Ibérica. En su planta piloto se mezclaron y fundieron los copos pretratados de EPS con material virgen de poliestireno y se sometieron a descontaminación por exposición a temperatura y vacío en condiciones especiales, obteniéndose granza de r-PS (poliestireno reciclado).
En la tercera fase, esta granza de poliestireno con diferentes porcentajes de material reciclado se envió a la planta de producción de Coexpan. Las distintas muestras de material fueron procesadas industrialmente para obtener la lámina extruida y posteriormente los prototipos de envases termoformados con contenido reciclado.
La operativa de las tres fases han sido evaluadas con la colaboración del centro tecnológico Aimplas, demostrando que los envases obtenidos de r-PS serían inocuos y seguros para su uso en aplicaciones de contacto alimentario.
Fuente e imagen: http://www.life-eps-sure.com/el-proyecto-de-innovacion-life-eps-sure-2017-2020-demuestra-un-gran-avance-en-la-economia-circular-de-los-plasticos/